ATOMIZATION DRYING PROCESS
The product to be dried comes from the feeding tank, then it goes through the filter and is transported by a bomb, after that it goes through the feeding group reaching the atomizer disk distributor.
The drying air is heated up by the burner in the direct oven, through the conduit it is distributed by the disperser and gets in touch with the product cloud produced by the atomizer disk. The drying happens inside the chamber, coming out into the interconnect conduits and getting to the powder recovery hurricane.
All of gases are aspirated by the fan and thrown in the atmosphere through the chimney.
The powder eventually deposited in the chamber walls is loosened by the vibrators.
Through the rotary valve the product is collected, and it can be wrapped or stocked according to its final destination.
The gases and small colloidal particles dragged by these gases go through a venturi that compresses them. It moisturizes them so that they are incorporated into the water that is being circulated by a centrifuge in the washer.
The equipment has a support and a cut for the correct maintenance and atomizer cleaning.
Basic Introduction to Drying Process
Some items are indispensable to obtain a complete view of ours dryes.
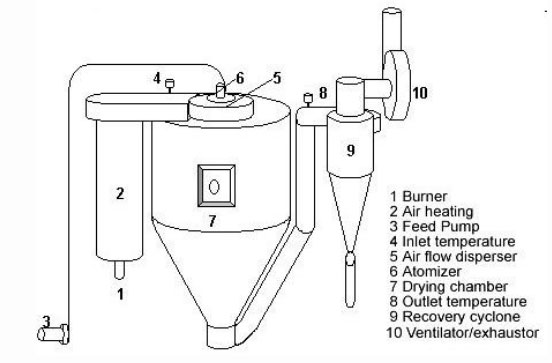
- High drying air flow rate leads to a fast dislocation of product in the chamber, with increase of residual humidity.
- Low drying air flow rate leads to a long permanence of product in the chamber, which results in a very dry powder.
- High air speed leads to a good separation of product in the cyclone.
- High air speed leads to a good separation of product in the cyclone.
- High air speed leads to a good separation of product in the cyclone.
- Low concentration of product and high speed of atomizer disk result in very small particles of product, making it more difficult to obtain a good cyclonic separation.
- With very small and fine particles, the extraction has to be done with manga type filters.
- When the air flow rate of the Feed Pump increases and the inletl temperature remains constant, the outlet temperature decreases.
- Inlet temperature is equal to air temperature that enters in the drying chamber, which is introduced through the air disperser, by a ventilator/exhaust, and encounters the pulverized product, making the vaporization.
- The final product (solid) is not submitted to the inlet temperature. The temperature of drying air mixed with the solvent vapors and the dry material, before entering in the cyclone, is denominated outlet temperature.
- This temperature is not necessarily the temperature of the dry material, which goes relatively cold, according to the residence time in the equipment. Therefore, outlet temperature can be considered the highest temperature that the final product could reach with a slow process of recovery.
While the inlet temperature is controlled only by the burner, the outlet temperature is controlled by the following parameters:
- Inlet temperature
- Air flow rate
- Air flow rate of Feed Pump.
- Concentration of product to dry.
- One of the most important points to consider in drying by atomization is the optimum difference st between the inlet temperature and the outlet temperature, which is called .
-Increasing the difference at of temperature by raising the amount of product entering in the chamber and keeping the inlet temperature constant, the residual humidity of the final product will raise.
- One of the most important points to consider in drying by atomization is the optimum difference at between the inlet temperature and the outlet temperature, which is called .
- Dryer with indirect air heating utilizes the same gases of combustion, of liquid or gas fuels, to heat the drying air. This mixture contacts the product directly.
- Dryer with indirect air heating can utilize any thermal source to heat the drying air.
-In indirect air heating can only enter atmospheric hot air and or previously filtered air.
- For a correct performance of drying by spray, the dosage of product has to be uniform (not pulsing) and controlled by microprocessor constantly. The correct gradual variation of dosage makes the equipment to work in continuous periods, without eventual interruptions.
Men's Houston Texans '47 Brand Navy Blue Stacked Logo V-Neck T-Shirt,Women's San Diego Chargers Navy Blue
cheap jerseys Cameo Knit Pants
SPRAY PROCESS
Estrada do Itaqui, 711 – Jardim Nova Itapevi - ITAPEVI – SP

Spray Process © 2009